Digital Twin
Digital Twin
Provide insights into the condition of equipment
What is digital twin
A digital twin is a virtual representation of a physical product or process, used to understand and predict the physical counterpart’s performance characteristics. Digital twins are used throughout the product lifecycle to simulate, predict, and optimize the product and production system before investing in physical prototypes and assets.
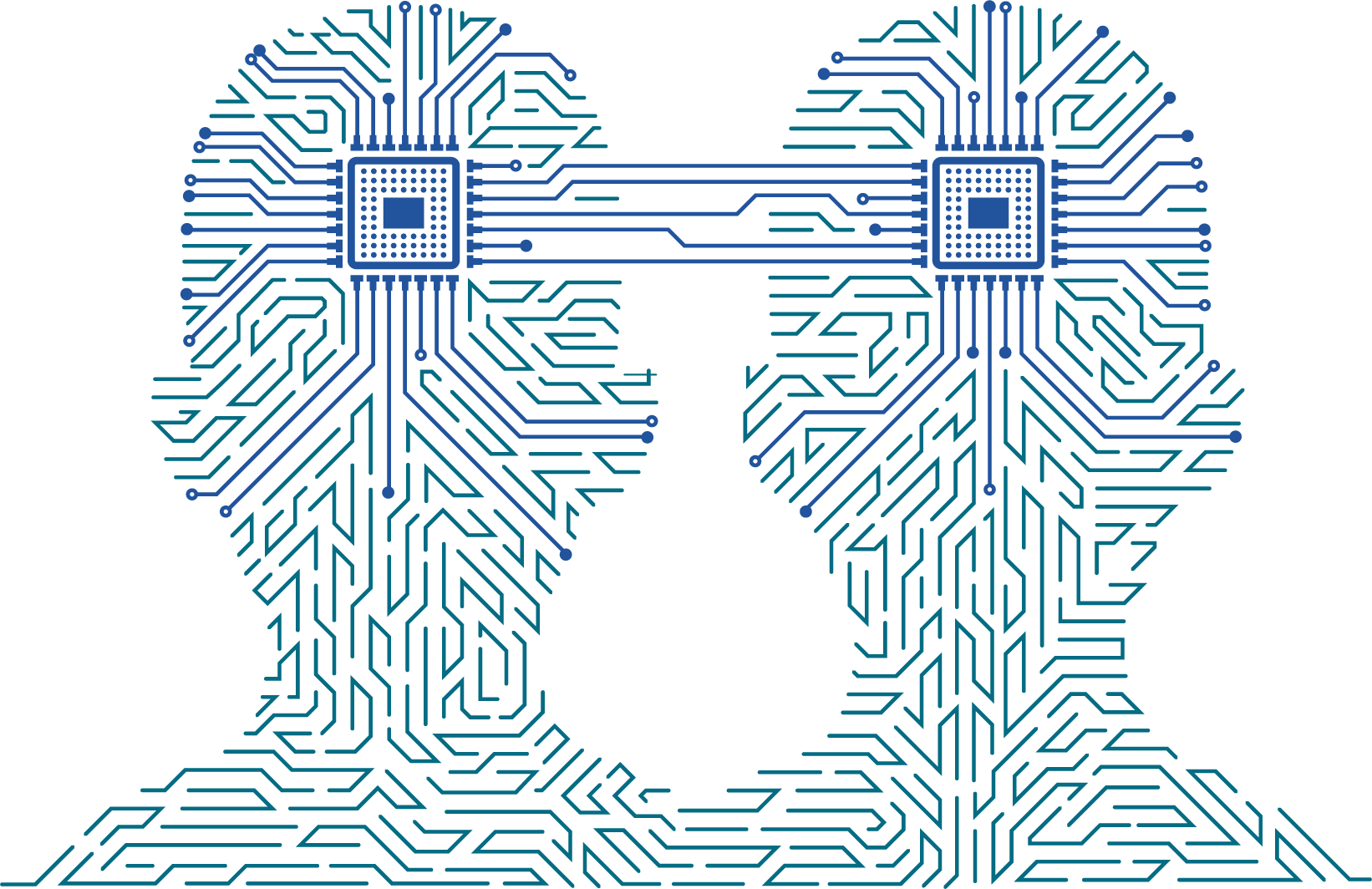
How we implement digital twin
For efficient design of new products
New designs and solutions can be verified through digital twin. Digital twin helps test products or working process prior to official launching, which reduce operational risks.
In manufacturing & production planning
Use digital twin as a real asset through the project can predict virtually operations and fulfil analytics-based maintenance.
To capture, analyze, and act on operational data
The model can be established by digital twin. Data of history and present can be collected to help detect problems in advance, correct errors quickly and create new, more reliable versions.
Things enabled by digital twin
Failure Prediction
Build an accurate model and powering with IoT data, the model can record the health and working conditions of devices, as well as learn from historical data to predict future failure predication.
Anomaly control
Digital twin helps integrate operational data of equipment. From data knowledge, we can detect anomaly, recognize failures, and diagnose failures by provide potential reason of failures to support and guide our clients’ operations.
Reduction on maintenance costs and operational downtime
Digital twin ensures the ability to build a rich database with AI-powered models. Clients will get industrial insights in real time, focus on operational process and do the right decision. This helps significantly create the positive outcomes.
How digital twin works in manufacturing
To ensure accurate modelling over the entire lifetime of a product or its production, digital twins use data from sensors installed on physical objects to determine the objects’ real-time performance, operating conditions, and changes over time. Using this data, the digital twin evolves and continuously updates to reflect any change to the physical counterpart throughout the product lifecycle, creating a closed-loop of feedback in a virtual environment. As AI, image recognition and other technologies advance, digital twins will adapt to them and develop exciting new applications for various industrial manufacturing.
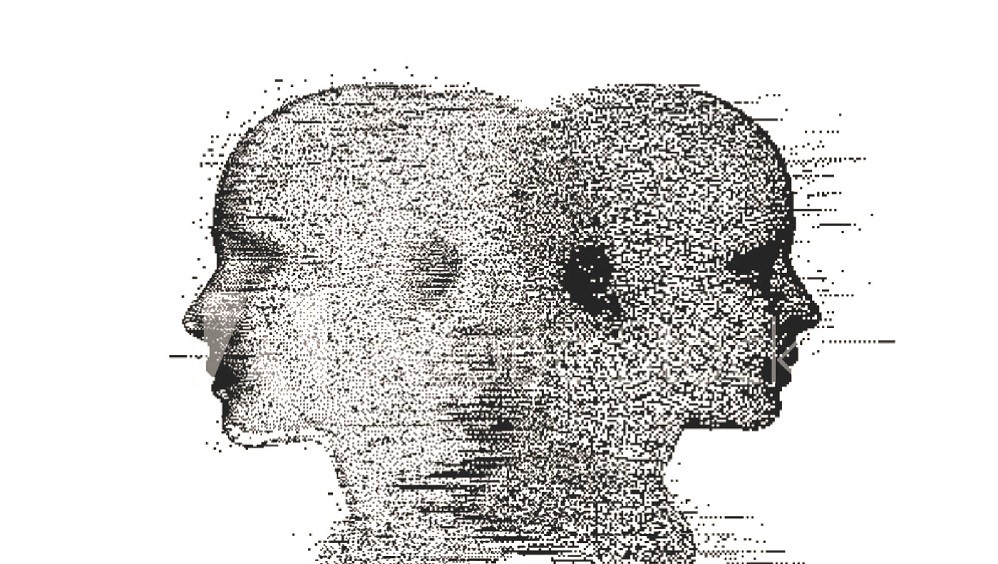